Choosing a Manufacturing Execution System (MES) for discrete manufacturing such Aerospace and Defense is a critical decision that can significantly impact your company’s operational efficiency and competitive edge. With the pressures of project deadlines and the need to stay ahead in the fast-paced manufacturing industry, making the right choice is crucial. Thankfully, you’re not alone in this process. By leveraging industry insights and following best practices, you can make an informed decision that aligns with your company’s strategic goals. Here’s how to get your MES selection right the first time.
Define Program Goals
Before diving into product demonstrations and vendor meetings, it’s essential to clearly define your business and project goals. An MES implementation is more than just adopting new software; it’s an opportunity to re-evaluate and optimize your entire manufacturing process. Whether your focus is on quality in aerospace and defense manufacturing, lean initiatives, enabling a digital thread, becoming a model-based enterprise, or ensuring regulatory compliance, linking your MES project goals with your broader business objectives is the first and most critical step.
By understanding your specific needs, you can better assess how different MES solutions will help achieve your desired outcomes. Some key goals to consider include:
- Boosting Productivity and Lean Manufacturing: Streamlining processes to reduce waste and improve efficiency.
- Enhancing Quality to Reduce Scrap and Rework: Implementing rigorous quality controls and continuous improvement practices across your aerospace and defense supply chain.
- Meeting Regulatory Compliance: Ensuring adherence to industry standards and regulations.
- Enabling the Digital Thread: Creating a connected, data-driven manufacturing environment.
- Consolidating Legacy and Disparate Systems: Replacing outdated systems with a unified MES platform to reduce your software debt.
Assemble the Right Team
The success of your MES project hinges on the team you assemble. This isn’t just an IT project; it’s a cross-functional effort that requires input from various departments, including Operations, Manufacturing Engineering, Quality, Production Control, and Inventory Management.
Start by securing senior-level sponsorship. Having executives as champions of the project ensures that the MES initiative aligns with long-term business strategies and secures the necessary resources. In addition to a strong project manager, include subject matter experts (SMEs) from each relevant department. Their insights will be invaluable in understanding the unique needs and challenges of your manufacturing processes.
Given the complexity of MES implementations, you may also need to bring in external consultants or systems integrators. These experts can provide specialized knowledge and help manage the intricacies of the project, reducing the risk of setbacks and ensuring a smoother rollout.
Understand Industry-Specific Requirements
While many MES solutions offer similar core functionalities, the specific needs of discrete manufacturing require a more tailored approach. In complex discrete manufacturing, technicians represent 20 to 60 percent of the cost of assembly. Unlike consumer electronics, where the quantities may be in millions, in complex discrete usage there are often quantities of one: a submarine, a helicopter, an MRI machine. One unit may go through well over 50 engineering changes from start to release. This is not seen in any other industry.
Consider an aircraft carrier. When one is built, by the time it has been delivered to the Navy it has been completely redesigned. That one ship has gone through seven complete electronics redesign cycles and builds, on average. Why? Technology evolution outpaces production. It takes three years to deliver an aircraft carrier or a submarine, and every time technology advances faster than the build process, they’re completely reengineered. The MES must communicate these ongoing changes to the shop floor technician efficiently and understandably as a priority. Therefore, it’s crucial to choose an MES that caters specifically to the demands of complex discrete manufacturing, rather than one designed for continuous or batch production.
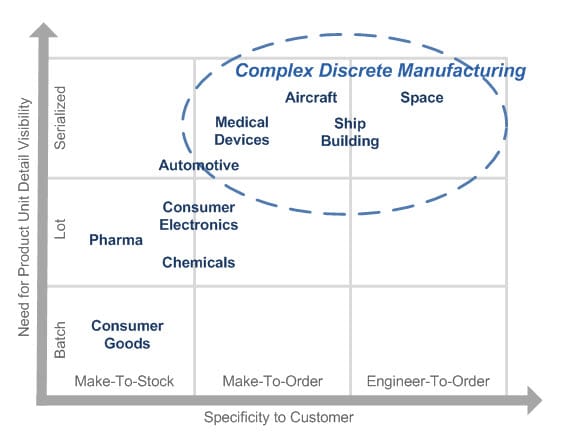
When evaluating MES providers, look for those that offer industry-specific functionality and support frameworks such as ISA-95 and ISO9001/AS9100/ISO13485. These frameworks not only provide a structured approach to manufacturing operations but also ensure that your processes are aligned with industry best practices and standards.
For example, the ISA-95 framework offers a standardized approach to integrating MES with other enterprise systems, while ISO9001 provides guidelines for implementing a robust Quality Management System (QMS). By considering these frameworks together, you can create a cohesive strategy that addresses both manufacturing execution and quality management, ensuring nothing falls through the cracks.
Leverage a Purpose-Built MES
Both your manufacturing execution system (MES) and your enterprise resource planning are important parts of your business. Both help improve your operations; no one denies this fact. But these are two different systems built for different reasons.
An MES, and more specifically, Solumina from iBase-t, was architected to meet the needs of complex discrete manufacturers; those that produce products with multiple levels of sub-assemblies, frequent engineering changes, and stringent regulatory requirements. In fact, Solumina is the necessary axis between your product lifecycle management and your ERP. It is transaction-based like an ERP, but with a focus on shopfloor activity that is much narrower and deeper than what your ERP can provide. An ERP integrates different functions across the business, such as finance and human resources. It was never intended to provide the level of detail to the operations team that an MES can.
Follow the Process
Selecting the right MES for discrete manufacturing is a complex but manageable task if approached systematically. By defining your business goals, assembling a capable team, and understanding your industry’s unique requirements, you can narrow down your options and make an informed decision.
To further streamline your MES selection process, consider using a checklist to evaluate potential solutions. Ensure each provider meets your essential criteria before moving on to more detailed evaluations. With the right MES in place, your company will be well-positioned to improve efficiency, enhance product quality, and maintain a competitive edge in the evolving manufacturing landscape.