Manage The Execution Of Complex Operations
Built for complex discrete manufacturing in the most demanding industries, Solumina MES software by iBase-t is designed to play a central role in your digital transformation. Part of the iBase-t suite of solutions, Solumina MES helps to tightly integrate all Industry 4.0 devices and software to become a digital ecosystem of technology and a unified source of data for your enterprise.
Gains Driven by Solumina MES
- Improved process collaboration across production, quality, and engineering workflows
- Improved operational agility
- Paperless operations and avoidance of manual processes
- Ease of reporting, tracking, and traceability of production processes and materials
- Standardized production processes and workflows
- Closed-loop quality management
Solumina MES by iBase-t
Take control of your manufacturing operations with Solumina MES.
Better Visibility and Control
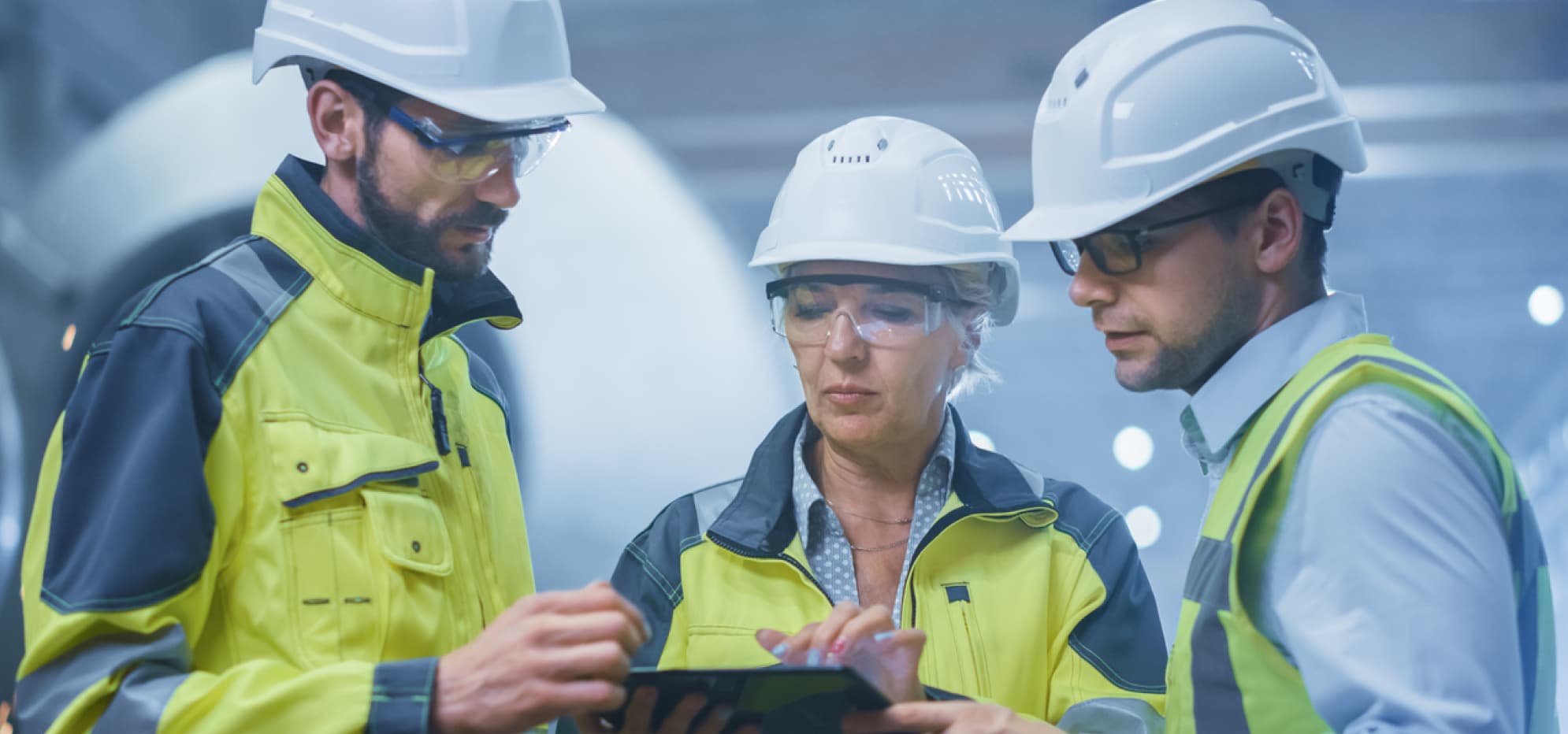
In complex discrete manufacturing, where value chains may span multiple locations and geographies, operations can easily become siloed. Operational performance data can be difficult to track, and frequent engineering changes and version control issues add further complexity. The Solumina MES solution was built for companies that manufacture complex products with multiple levels of sub-assemblies and frequent engineering changes.
Solumina clears the fog by driving visibility and control over every operations process. With a modern microservices architecture and open APIs, it can be deployed on the cloud, on-premises, or as a hybrid implementation. Pre-configured, best-in-class production process libraries and full device support accelerate time-to-value.
What Does a Manufacturing Execution System (MES) Do?
By facilitating the integration of manufacturing floor systems with engineering and business systems, an MES streamlines processes that span across the organization.
An MES gives enterprises real-time control for monitoring and managing all work-in-process (WIP) on the shop floor. It tracks and documents the transformation of raw materials through finished goods.
In digital enterprises, MES solutions connect shop-floor automation systems to the overall enterprise software network. The best solutions can tightly integrate with every other enterprise system, creating a digital ecosystem that coordinates quality management, planning, scheduling, dispatching, and production execution.
Take Advantage of the Key Features Solumina MES Has to Offer
Solumina MES manages your organization’s data and processes, updating them with real-time information.
Most importantly, it connects with your entire extended enterprise, including all suppliers, contractors, and business partners.
Complex manufactured products with hundreds or thousands of components and subassemblies need an MES solution that functions beyond the four walls of the enterprise. Solumina does just that.
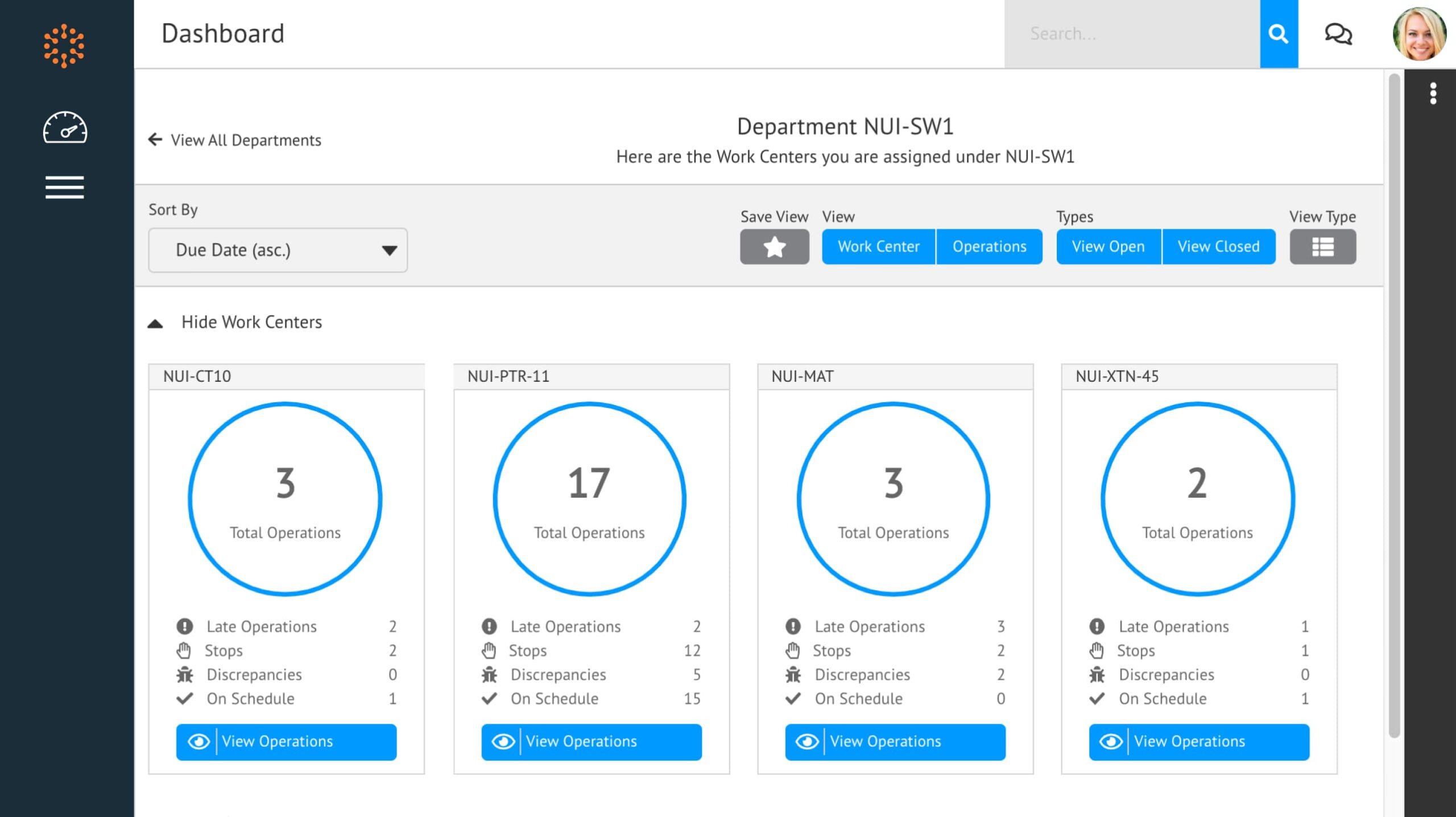
Resource Management
Solumina MES manages all resources in real time. It sorts machine and tooling compatibility, evaluates machines for preventive maintenance, and enforces proper tool calibration. It ensures that machines are set up and maintained correctly. Additionally, it can track materials and parts coming from other suppliers to initiate every process at the right time.
Production Definition Management
& Dispatch
& Dispatch
Solumina MES is the central manager for all BOMs involved with a product, including eBOM and CAD models. It manages the transformation from a manufacturing BOM to an engineering BOM and helps to keep production running smoothly by updating process plans with product updates in real time.
Product Tracking & Genealogy
In complex manufactured products with many parts and subassemblies, it is critical to ensure that the right parts are in place at the right time. Solumina MES software tracks all materials, parts, and components as they move from one work center to the next and transmits WIP inventory levels back to the ERP system. Solumina also maintains a complete product history, from ideation, into the customer’s hands, through to its disposal.
Performance Analysis
Solumina MES makes data accessible and contextualized so you can easily analyze and optimize business performance. Data is consolidated on dashboards with reporting tools so that executives and supervisors are working from the same source of information, updated in realtime from the factory floor. Track product cycle-time, resource utilization, and conformance to scheduling. Solumina can also include supplier data to track the performance of external suppliers.
Process Execution Management
Solumina MES enforces proper workflows and manages overall production. It is the central manager to make sure that every technician completes every step with proper calibration, tooling, and data collection. Solumina provides up-to-the-minute updates to work instructions, giving technicians graphics and text to guide through the work process.
Process Definition Management
Complex manufactured products are defined by the many processes involved in production. Solumina MES allows organizations to update new process instructions and engineering changes to work orders on the shop floor in real time, worldwide.
Data Collection
Data management is at the center of digital transformation. Modern production processes produce vast amounts of data, from design to compliance traceability. Solumina MES helps organizations funnel their data into a single source of truth for each manufactured product.
Quality Management
For many manufacturers, there is increasing demand for products to be delivered in record time. Balancing this rising demand with quality and traceability requirements is especially challenging in complex industries. Solumina MES helps organizations meet traceability requirements by documenting all as-built information down the entire tree of production, giving users access to a real-time single source of data to enforce quality control and mitigate risk.
Change Management
Solumina MES is a key resource for managing process changes. It enables enterprises to rapidly deploy new processes to multiple production lines and plants, ensuring that all workers have the proper instructions and that production schedules are maintained.
“The Solumina Manufacturing Operations Platform creates the technology infrastructure manufacturers need to harness advances in model-based functionality.”
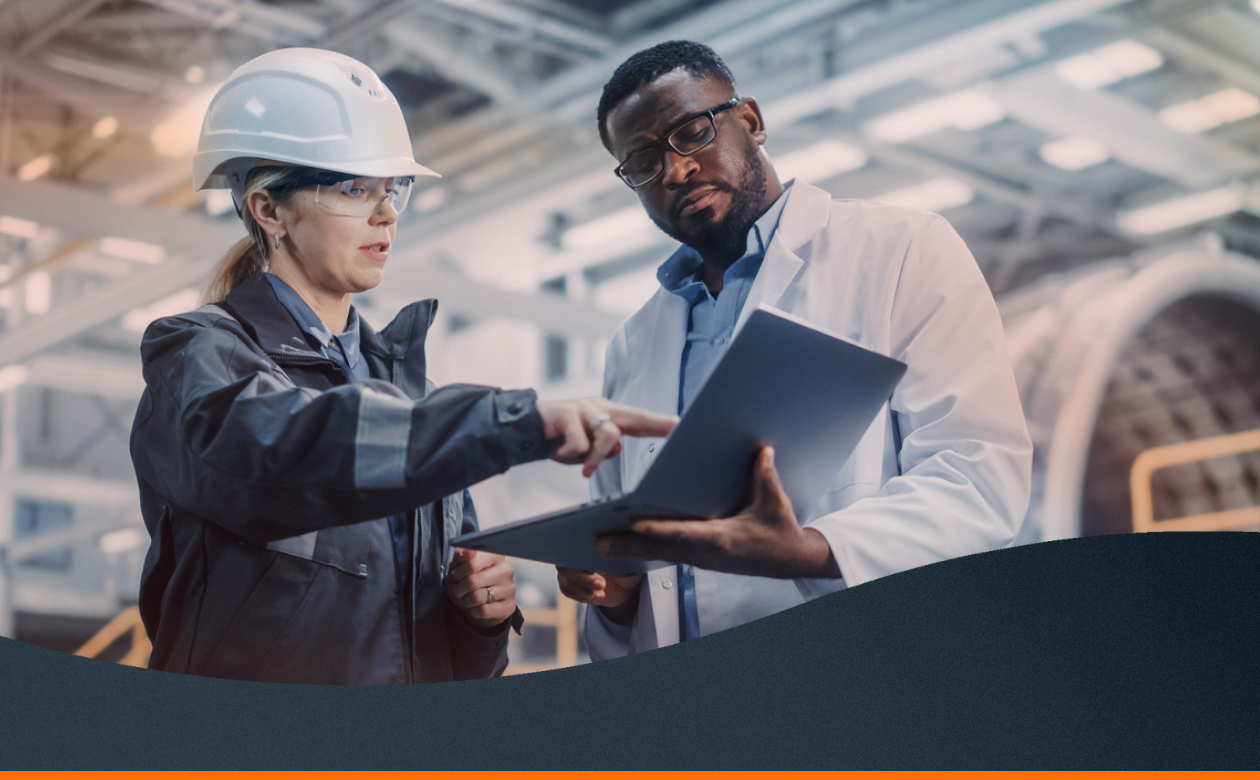
Solumina MES Brochure
Solumina Manufacturing Execution System (MES) by iBase-t enables new levels of visibility, velocity, and control for complex discrete manufacturers. Take a deeper dive into Solumina with this shareable brochure.
Benefits of Solumina MES
MES is a top manufacturing investment priority. Surveys by Gartner and LNS Research found that 68% of manufacturers saw MES as part of their enterprise systems strategy.
Solumina MES delivers results quickly. Most organizations see results within the first three months and can expect to improve outcomes in net profit margins, on-time delivery, and total cost per unit.
However, the benefits go far beyond these short-term gains. The largest benefits come from capitalizing on the visibility Solumina MES provides into manufacturing performance and capabilities across the organization and supplier network. After the initial payoff, companies should expect a lifetime of business improvements, both internally and externally.
Efficiency Gains
Solumina MES updates data to all other systems in real time. It helps to avoid repetitive manual work and prevents errors due to translation. When integrated into other business systems, Solumina MES can be used for process optimization, in addition to process execution.
On-Time Delivery
Calculating an entire enterprise’s ability to meet delivery goals can be challenging. Solumina MES gives access to a digital model of the factory floor that provides visibility into the status of every process in real time. Each production unit can be traced on its way through different workstations, and into the end user’s hands
Actionable KPIs
Different manufacturers need different methods to calculate their KPIs. Solumina MES visualizes the flow of production with customizable, user-friendly dashboards and graphs. Process and engineering improvements are made possible by business-relevant KPIs that empower decision-making and optimization.
Managing People As A Resource
People are just as important to manage as processes. For a globalized, complex discrete manufacturer, there is a wide range of workers who are authorized for specific processes. Solumina MES integrates with systems such as Time & Attendance to coordinate the best possible scheduling and ensure the optimal utilization of workers.
Closed-loop Quality Management
Solumina MES centralizes all the data and processes needed for quality management. It makes the information accessible and helps to bring new products to market by navigating complex compliance requirements and traceability. Closed-loop quality management is needed to innovate and gain an edge over competitors.
Process Improvements
Process improvements are key to improving a wide range of attributes, including new product introductions, supply chain management, and cycle-time. Solumina MES makes best practices standardized throughout the global enterprise. As process improvements are made, they can be easily updated and spread through the rest of the organization, no matter the distance.
Better Outcomes And Continuous Improvement
Continuous performance feedback provided by Solumina MES supports integrative and sustainable improvement initiatives. It becomes easier to manage the end-to-end supply chain. Increased resource sharing and flexibility is enabled by standardized best processes across multiple production sites.
Comprehensive MES Is More Effective at Improving WIP Management
Beyond being simply a production execution application, a comprehensive MES like Solumina MES supports production process optimization. It connects shop-floor automation systems to the overall enterprise software network, helping manufacturers manage the full range of shop-floor activities that have direct or indirect impacts on WIP.
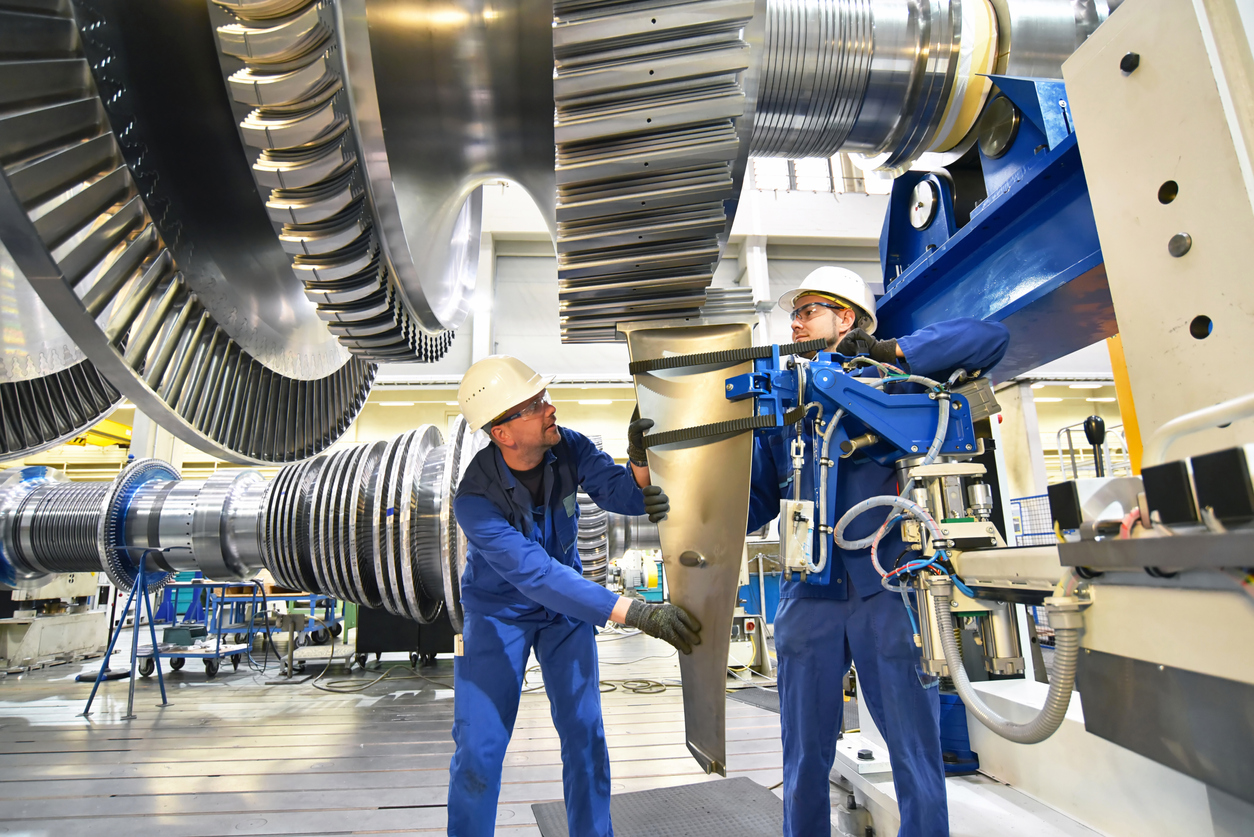
Why Should You Integrate Your MES and ERP?
Eliminate repeat data entry while turning ERP data into actionable information.
ERP is a system of record, while MES is a system of production, and they must work together to achieve optimal resource utilization. The MES-ERP integration orchestrates work orders with resource needs so that every business process is synchronized. The collaboration of business systems also means that data entry only needs to be done one time, which streamlines production by removing repetitive processes.
By tracking planned and current production progress, the MES ensures ERP information matches the real-time situation on the shop floor. Without an MES, ERP data can be unreliable due to manual errors or unaccounted losses. An MES brings in the information of the individual manufacturing process and design, turning ERP data into actionable information. This automates a process that is often done manually, improving both time and accuracy.
Why Should You Integrate Your MES and PLM?
Provide design engineers with real-time information from the shop floor to achieve continuous improvement in the design process.
PLM contains all the design information for the product and process. When PLM is integrated with MES, manufacturers can act on real-time product and process information. This creates a closed feedback loop between PLM requirements and variables from the shop floor during production, reducing the production of defective components.
When shop floor issues occur, PLM-MES integration allows faster isolation of the root cause, including issues in the extended supplier network. MES extends this integration out to suppliers for enhanced data exchange and communication.
“PLM-MES integration should be high on every manufacturer’s to-do list, because it leads to much bigger things – digital transformation.”
Director of Product Management, iBase-t
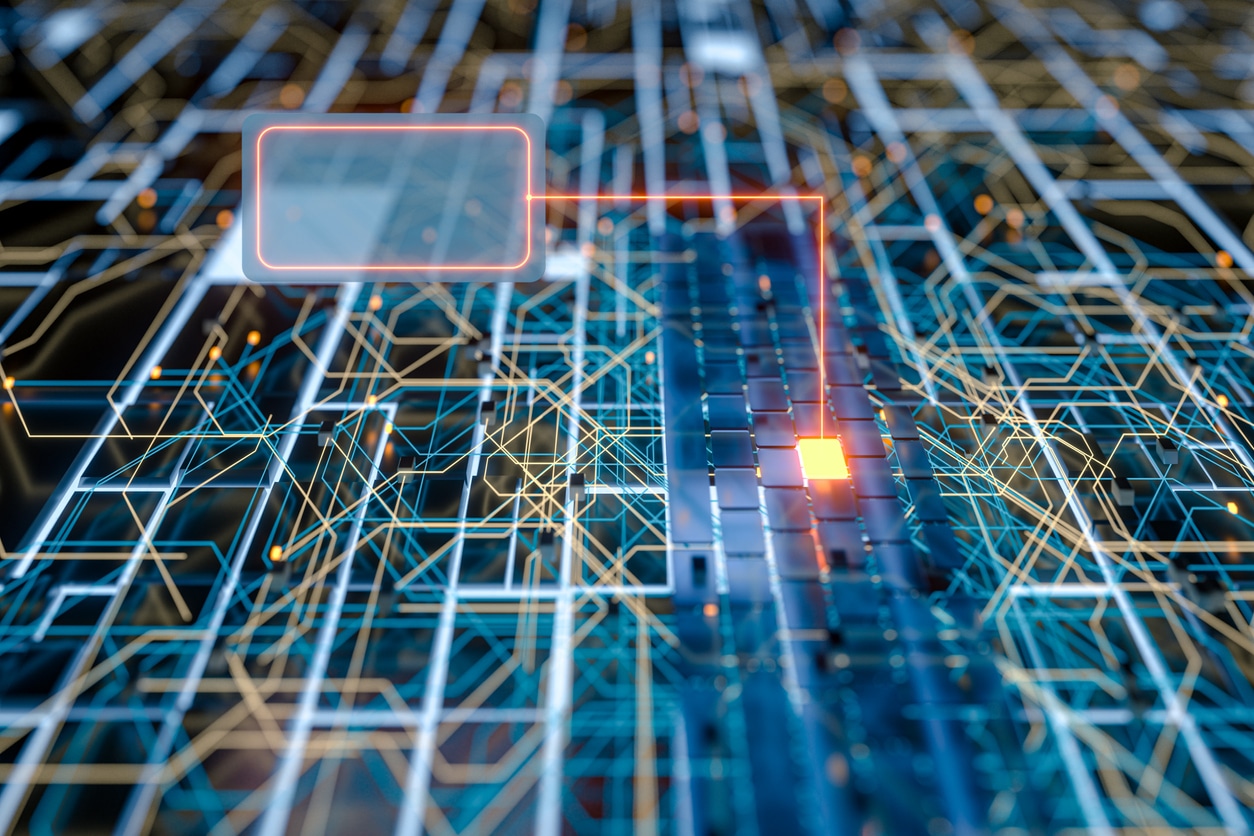
Why integrating MES and PLM should be at the top of your to-do list
PLM-MES integration is one of the fundamental steps on the path to smart factories, digital threads, and the Model-based Enterprise. Once MES and PLM are tightly linked, big things can happen.
PLM-MES Integration for NPI
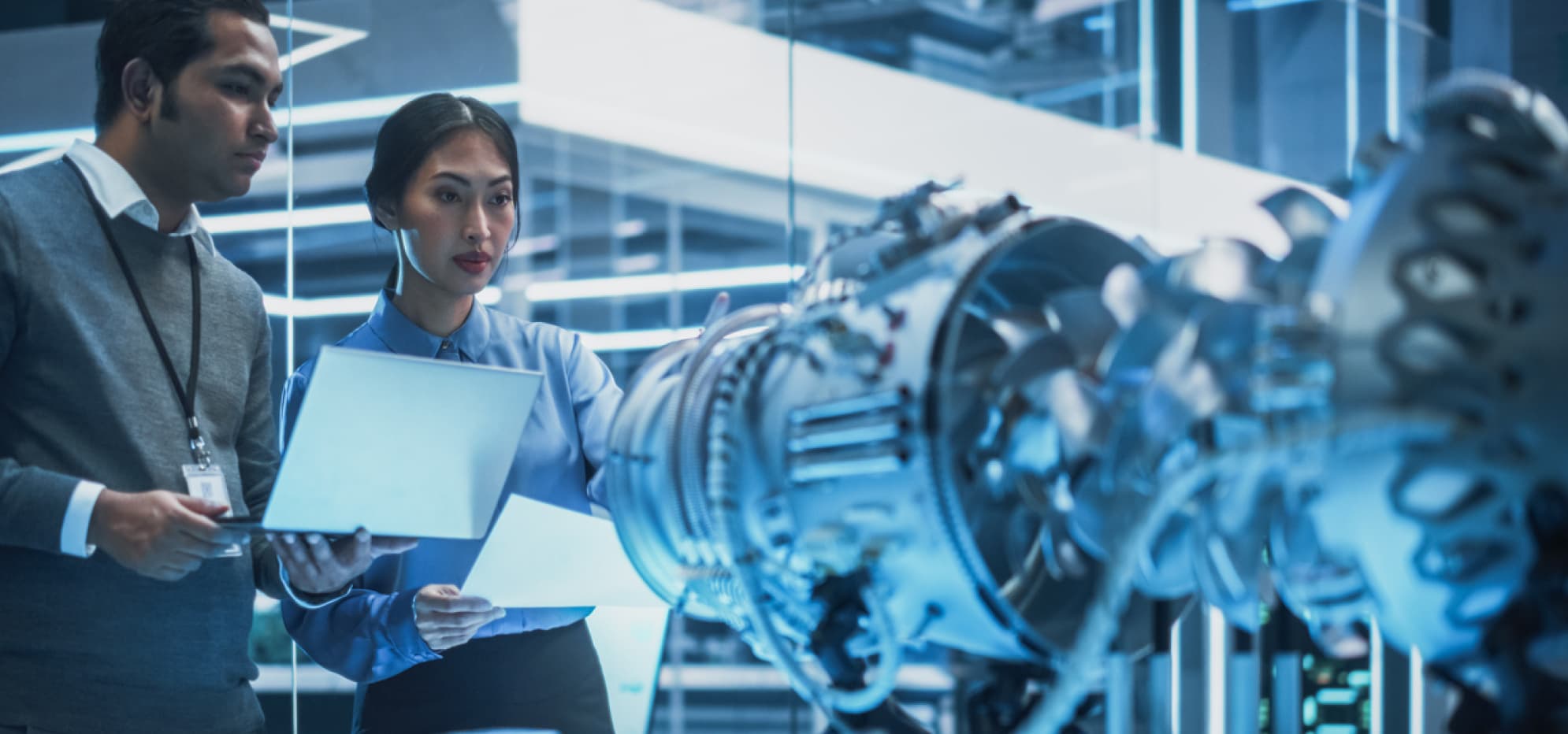
PLM-MES integration accelerates new product introduction (NPI) by evaluating process efficiency and optimizing the product process and design. It makes sense of the data created during the initial design phase, which manufacturers can then use to reduce cycle time, increase capacity, and standardize best practices. Additionally, the monitoring system helps to avoid unnecessary operations and rework to keep production processes sustainable.
Accelerating NPI is an increasing focus for many manufacturers looking to gain a competitive edge. For example, if the Pentagon is seeking contracts for production of a new aircraft, they are going to seek the best quality at the lowest price. That requires manufacturers to focus on product and process optimization. Improving NPI time-to-market helps manufacturers succeed in a competitive market.
Solumina MES Helps Achieve Quality Gains
Rapid technological changes are transforming the production of goods and services across the global economy.
As Industry 4.0 takes shape, complex manufacturers must keep their operations competitive and achieve quality gains. Solumina MES helps manufacturers break down information silos between departments, allowing closed-loop quality management by bringing quality data into one central location. Manufacturers can use this data for process optimization and proactive issue prevention. A central system accessible to all is key to closing the loop.
Solumina also ensures quality by enforcing proper procedures during production, including:
- Complex process routing sequences
- Engineering changes affecting WIP
- Collection of manual data entry, verifications, and signatures
- Personnel qualifications requirements
- Equipment and tooling calibration requirements
- Documentation requirements for a complete history of every unit
- Traceability of components/assemblies installed and materials used
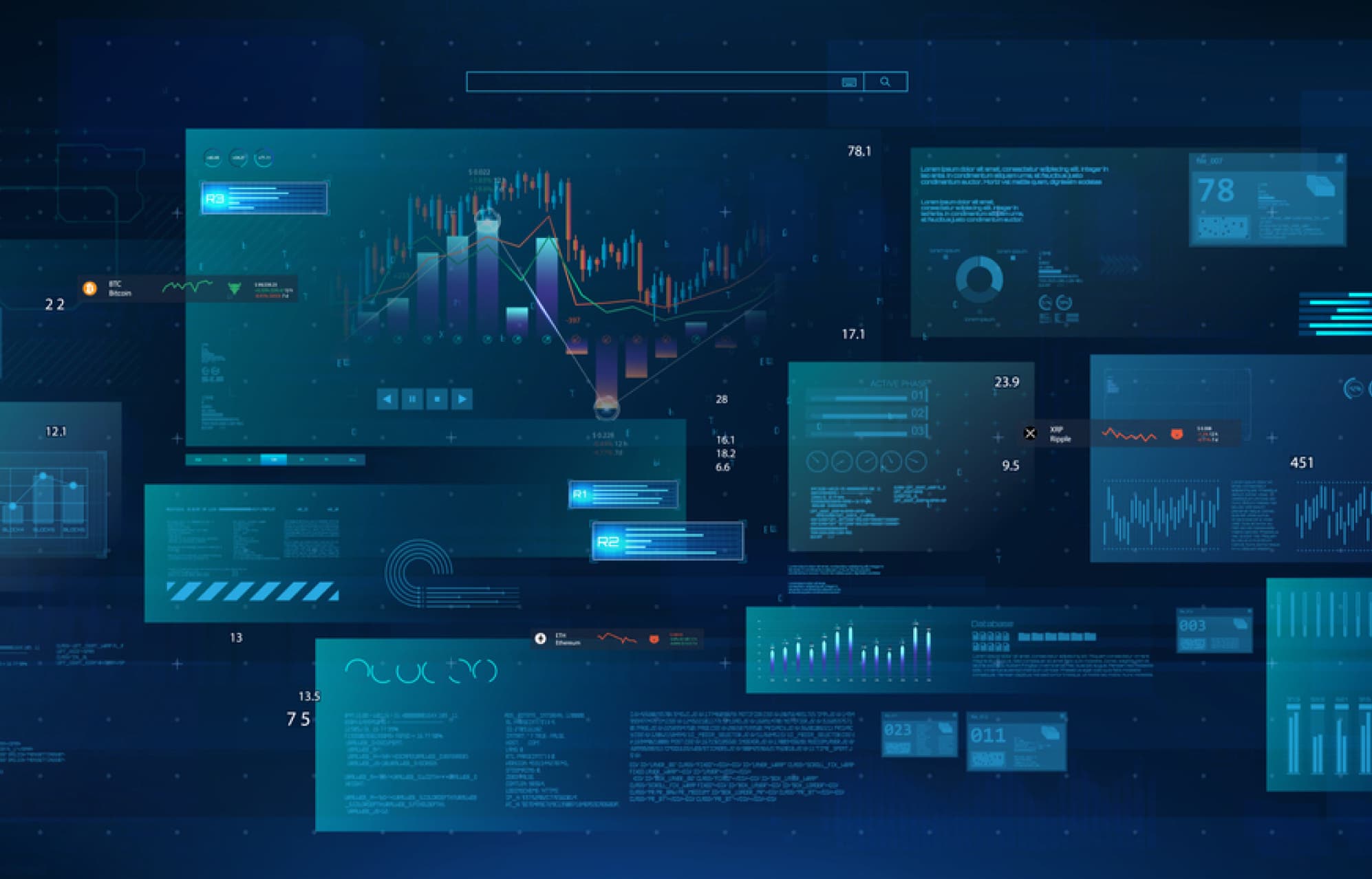
Solumina MES Provides the Foundation for Implementing a Digital Thread and Digital Twin
A digital twin is the virtual, real-time digital counterpart of a manufactured product or manufacturing process. It is used to achieve continuous improvement in model-based design and engineering processes.
The Digital Thread Is the Foundation for Digital Twin
It is a digital representation of a manufactured product’s design and specifications. It is used to view the status of connected devices, which updates data to the digital twin in real time. With this method, the digital twin is an accurate virtual copy of the device’s current status. Complex manufacturers can achieve better preventive maintenance and enhanced quality control capabilities with digital thread and digital twin.
MES for Complex Discrete Manufacturing
The economy’s most critical sectors— aerospace and defense, nuclear, medical devices, robotics, and industrial equipment— leverage complex discrete manufacturing.
These industries typically deal with strict regulatory and compliance requirements, making MES an essential technology for manufacturers seeking greater control, compliance, time-to-market, and visibility. Solumina MES manages product lifecycle execution with accurate instructions, real-time data, and manufacturing intelligence.
Solumina MES enables flexible routing optimized for order quantities and integrates non-conformance and deviation processes. It also provides serial tracking at suppliers and factories. It reduces paperwork by delivering greater accuracy, precision, and quality of online work instructions, while scaling processes across all production centers at any time, in any location.
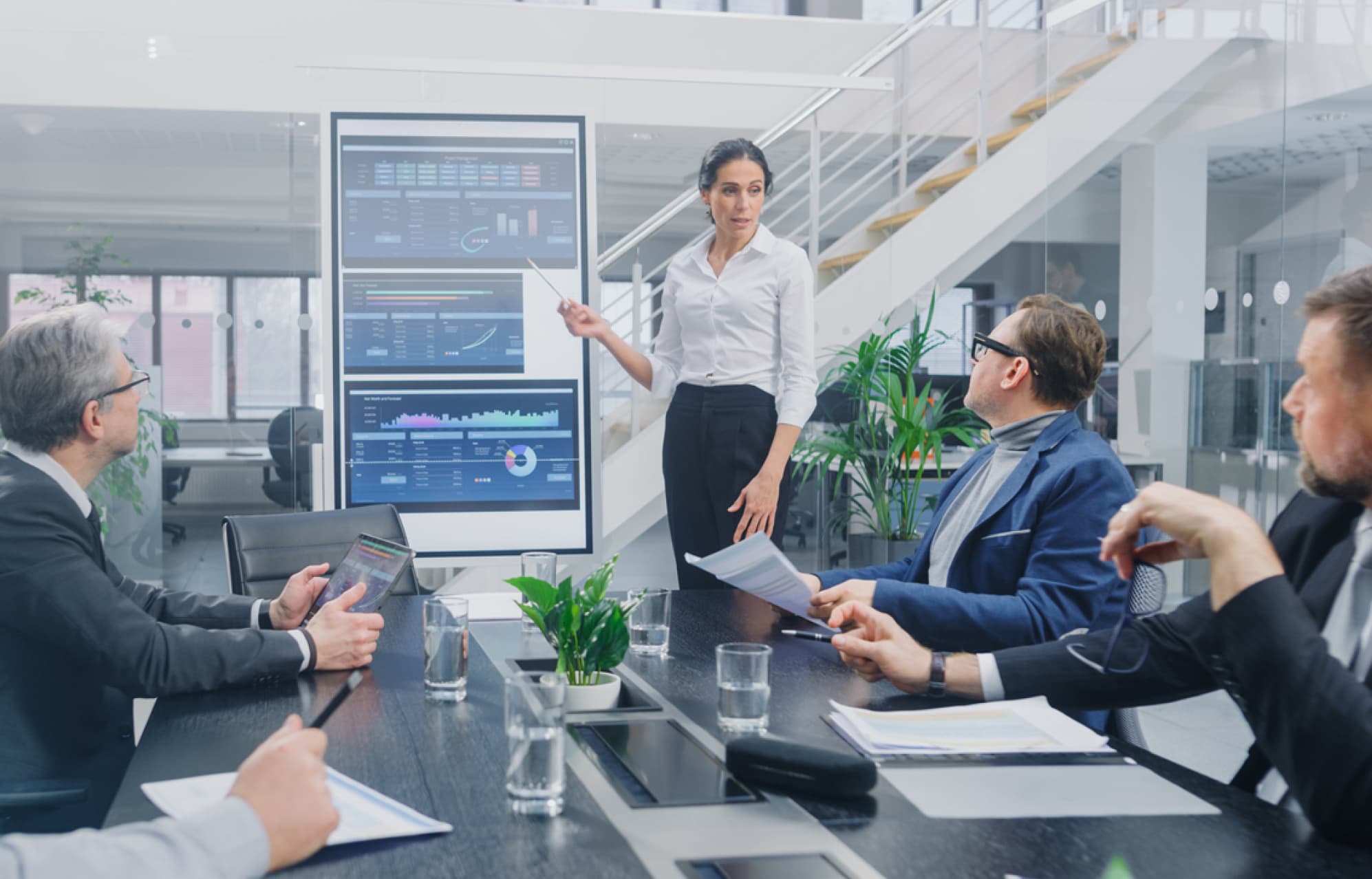
MES Helps Complex Discrete Manufacturers
Solve These Problems:
- Difficulty innovating to meet market demands
- Coping with the pace of change
- Latency of information: receiving data too late for useful analysis
- Issues with material traceability
- Poor visibility into WIP
- Missed production schedules
- Lack of production throughput
- Excessive errors due to paper-based or manual processes
- Too Many Systems on the Shop Floor: lack of a unified vision
Selecting the Right MES
Not all manufacturing software is equal. Each product and vendor will create a different experience with varying levels of functionality and scalability. A given system may be more or less than is needed for the individual manufacturer.
Modular architecture addresses this issue by allowing enterprises to pick and choose their MES functionality as needed, almost as simply as adding apps to an iPhone. This ensures that companies get the most out of their MES by giving the right functionality and integration for each circumstance.
Should You Choose Custom or COTS?
An MES can be custom built or commercial off-the-shelf (COTS). In making the decision, there are five important risk factors to consider:
Budget Risk
Unexpected work required in implementation services
Operational Risk
Insufficient hardware, lack of training, or flawed implementation
Change Management
The rate of user adoption and productivity within the organization
Technical Risk
Configuration problems and technical debt sending a ripple effect through the implementation process
External Risk
External factors, such as company consolidations and new strategy
COTs Is Less Expensive and Time-Consuming Compared to a Custom Solution
Many COTS users cite refined compliance in ready-made systems and lower maintenance costs as key advantages. While each option carries its own risk, the COTS approach is more predictable and involves fewer surprises. Custom solutions can seem like the best choice today for meeting exact needs but can become cumbersome and difficult to manage as the enterprise changes and evolves.
There are many factors to consider when choosing an MES implementation strategy. The strategy chosen will dictate the success of the transformation for years afterward. For manufacturers seeking to unify the vision of their enterprise and forge a path into the future of Industry 4.0, choosing the right MES and implementation partner is critical. See our white paper, Don’t Be Fooled by the Wrong MES, to learn more!
Additional Resources On MES for Complex Manufacturing
Learn What Solumina
Can Do for You With a Custom Demo