MES and Industry 4.0 Manufacturing
MES solutions are integral to digital transformation as big data coming from software solutions is driving manufacturing innovation.
Creating a Digitalized Manufacturing Ecosystem
Industry 4.0, or the Fourth Industrial Revolution, is the combination of various digital technologies—computers, enterprise software, the IIoT, machine learning, and big data analytics— to create a new, fully digitalized manufacturing ecosystem. Like the three industrial revolutions that came before it (steam power, electricity, and automation), Industry 4.0 is proving to be transformational.
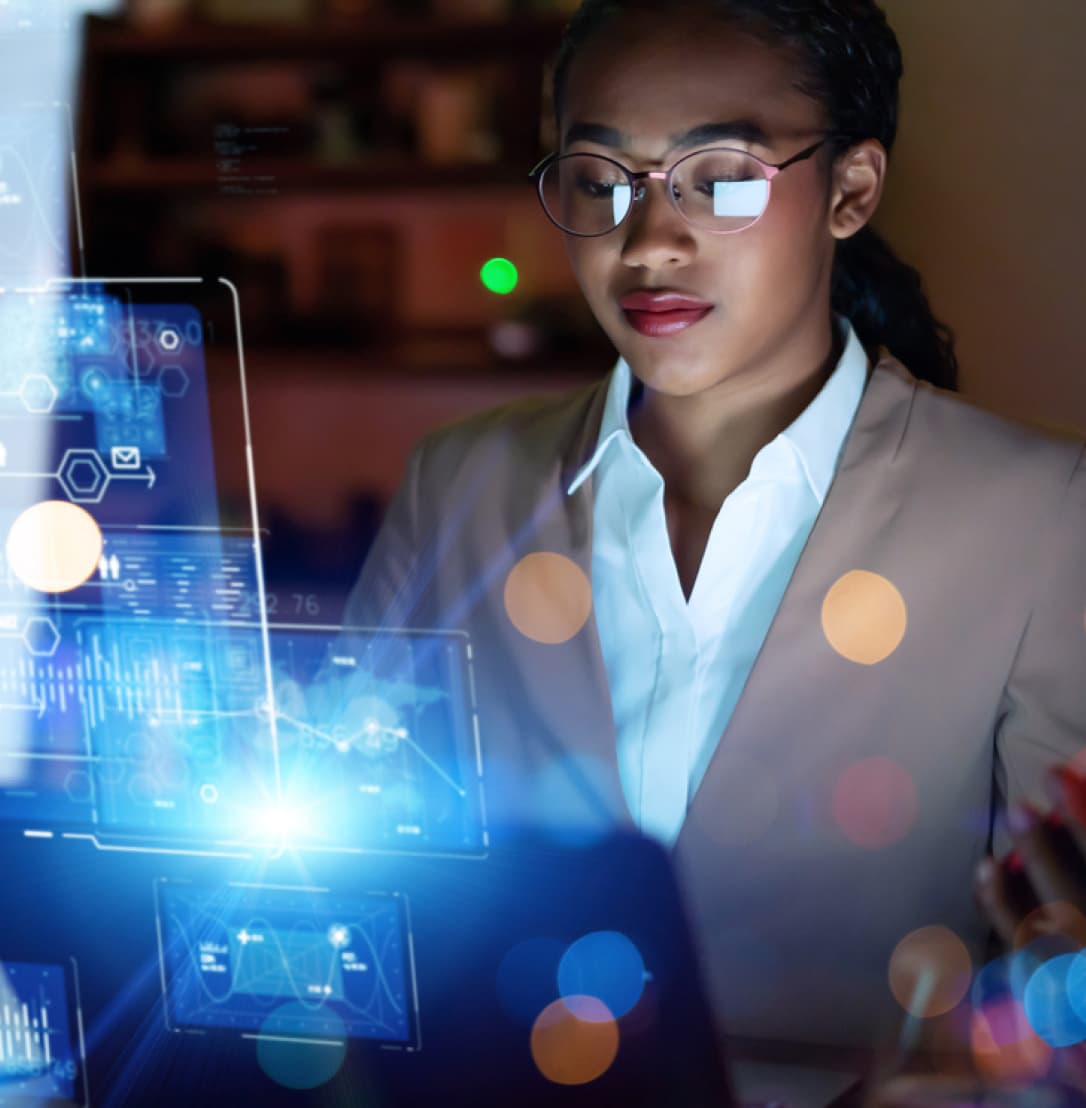
MES is at the center of Industry 4.0
The backbone of this new ecosystem is the Manufacturing Execution System (MES), which produces and gathers most of the essential manufacturing data. It also enables decision-makers to deploy changes in products, plans, and supply chains throughout the enterprise quickly based on up-to-date information. MES, implemented as part of an Industry 4.0 manufacturing strategy, turns a collection of disparate operations and into a well-oiled, digitally transformed machine.
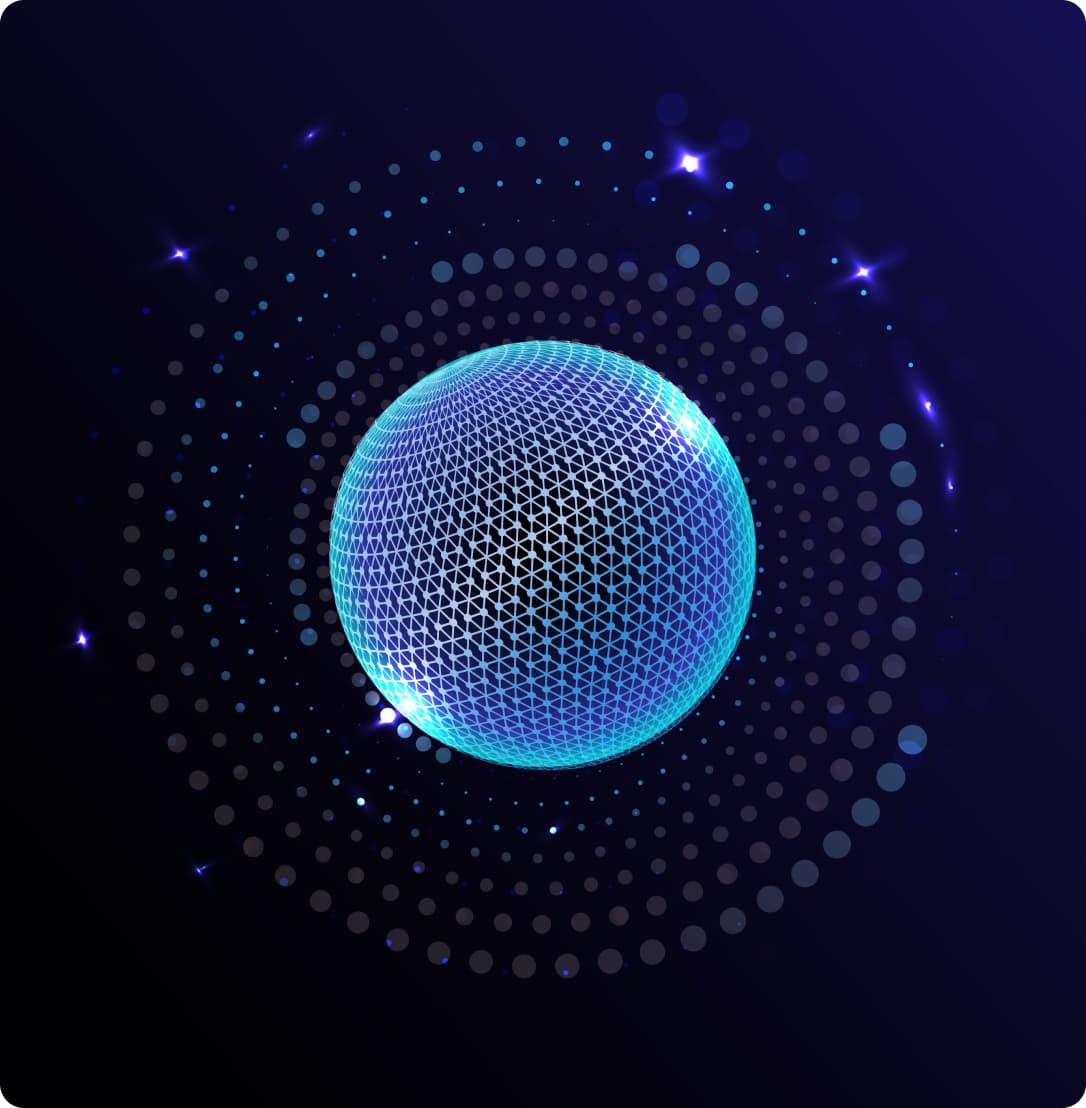
PLM-ERP-MES Integration
Connect data and systems spanning the entire manufacturing process, from enterprise business applications to shopfloor machines and tools.
Data Analytics Leads to Big Improvements
Data is arguably the most underused resource in the modern manufacturing enterprise. It also represents the biggest opportunity.
MES and IIoT-connected machines generate huge amounts of data, but it is not easy to collect and distribute it all to the right people at the right time. It’s estimated that the average factory generates as much as a terabyte of production data per day.
Big Data Analytics Software is the Perfect Partner to MES
Yet many organizations, especially those with disparate systems, can utilize only a small fraction of that data, and rarely to support actual operational decision-making.
This is why big data analytics software is the perfect partner to MES and a critical component of Industry 4.0 manufacturing. Big data refers to datasets that are too vast for typical database software tools to effectively capture, store, and analyze—which describes most manufacturing databases.
Achieving significant performance gains
With big data analytics, it’s possible to see trends and correlations in this data that would be undetectable to the human eye or to previous-generation software. By combining big data analytics with the agility of an MES-controlled factory floor, manufacturers are achieving significant performance gains in many areas.
Big Data Analytics Can Help Grow Your Operation By:
- Boosting productivity by up to 30%
- Reducing product development and assembly costs by as much as 50%
- Improving quality
- Significantly reducing capital costs
Industry 4.0 MES Integrates with Other Platforms and Technology
- Software technologies: AI, machine learning, analytics
- Production technologies: Robotics, controllers, assembly line systems
- Enterprise operational technologies: ERP, PLM, Supply Chain
- Infrastructure technologies: IIoT, Cloud
The Proactive Enterprise
Integrating MES with ERP and PLM systems creates a proactive enterprise, instead of a reactive one. ERP and PLM are not enough to accomplish this alone. Since they are primarily systems of record, they need integration with an execution system in order to effectively act on any of the information. Once integrated, factory managers can be proactive about ensuring the delivery of on-time, cost-effective products.
Closed Loop Integration
When integrated with both ERP and PLM, Industry 4.0 MES closes the loop between design, production, quality, and resource management, and provides a “single source of truth.” Everyone from the shop floor to the CEO can work from the same real-time data. PLM users can easily send engineering changes to the shop floor. Then, as resources are modified, the information is sent to ERP to avoid tedious re-entry of data. Closed-loop integration improves quality and change management across the entire value chain and product lifecycle.
Part of the drive for Industry 4.0 and digital transformation is to automate the collection, analysis, and distribution of data to make it available for dashboards and accessible to our citizen data scientists to go in and grab it, manipulate it, and do whatever they need for custom, high-value-added reporting.
Dr. Don Kinard
Senior Fellow, Lockheed Martin
A Powerful Communication Framework
The digital thread is a digital model of everything about a product’s lifecycle: design, manufacture, process, quality inspection, even post-delivery maintenance and operations. Learn More
Quality
Velocity
Change Management
Data Accessibility of an Industry 4.0 MES
Data accessibility is a primary goal of industry 4.0 MES. With contextualized and distributed data, executives and managers have the information they need to make the right decisions.
Accessibility includes being able to see the data needed from any tablet, smartphone, or computer terminal. But it also means much more. Manufacturers need clear visualization of data with multi-dimensional and real-time information on process variables. Industry 4.0 MES unifies all data so that executives, managers, and line workers are all working from a single version of the truth, with information contextualized for their use.
Cloud Accessibility & Security
Cloud-based applications make it easier to distribute and access manufacturing data. They lighten the load on technical debt by reducing hardware and ensuring smooth software upgrades. Many organizations need to keep the most sensitive information on premises. Industry 4.0 MES does not dictate the implementation; it allows the deployment of Industry 4.0 software technology on the cloud, on premises, or both, as needed for their circumstances.
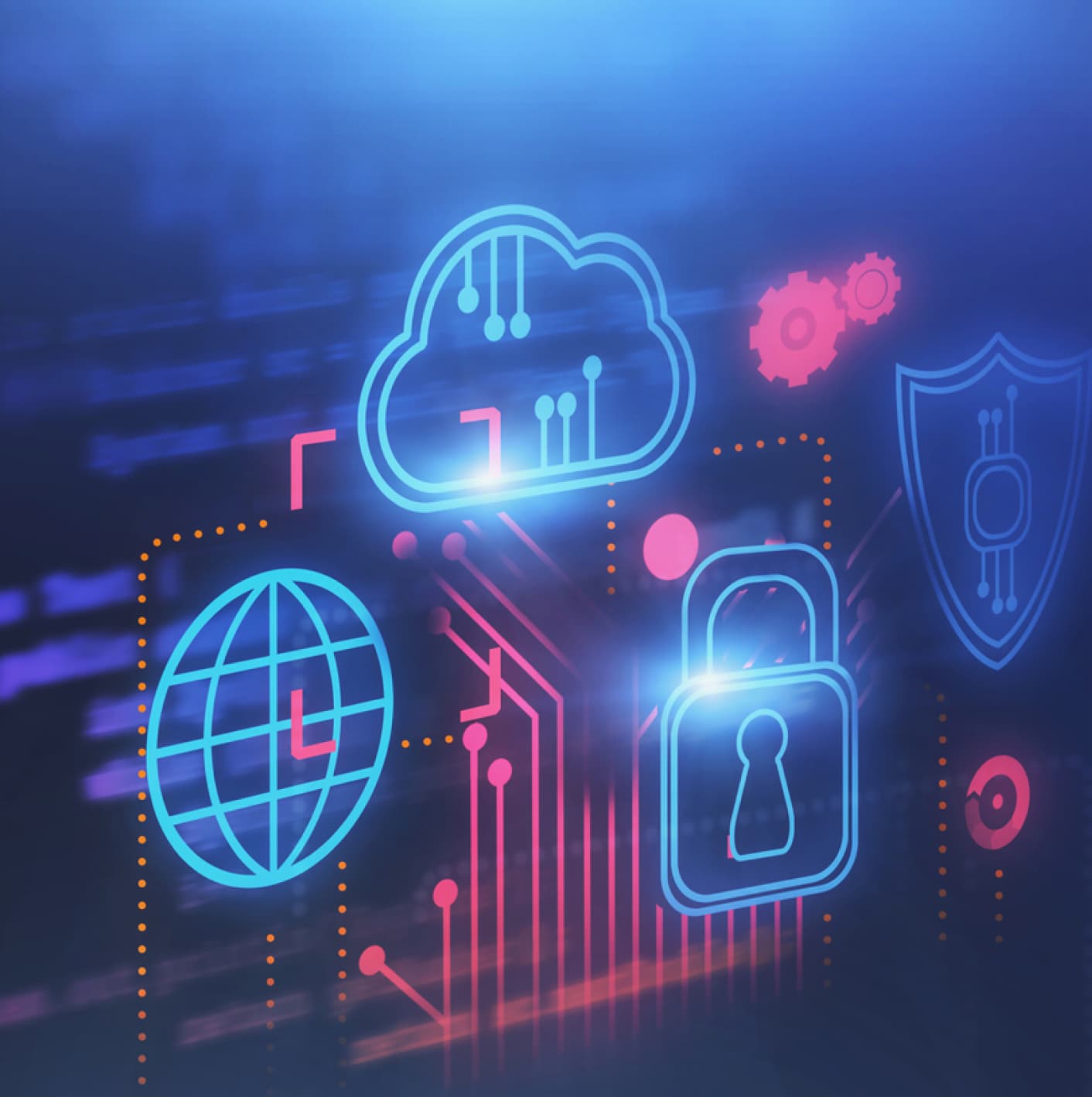
Efficient Data Analytics
Big data analytics demand extraordinary levels of processing power. Industry 4.0 MES allows users to export data to cloud-based big data structures to efficiently distribute operational data. The result is contextualized data that organizations can use to respond to changing conditions.
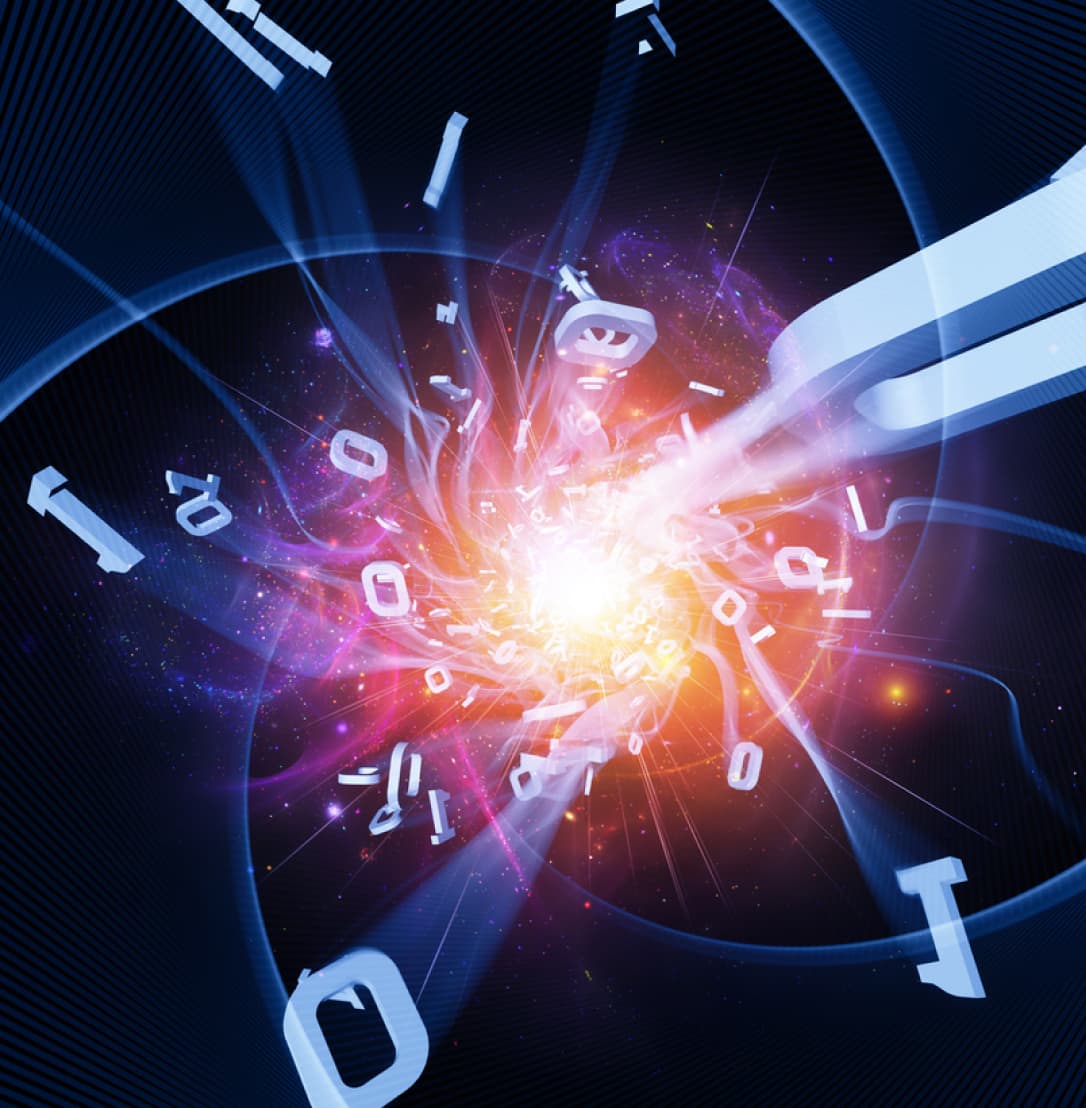
Process Optimization
Data accessibility optimizes production processes by standardizing process improvements. It ensures that business decisions are based on up-to-date production information, with contextual data to anticipate its impact on the supply chain or product lifecycle. Simultaneously, machine learning enables systems such as MES to keep pace with changes in production.
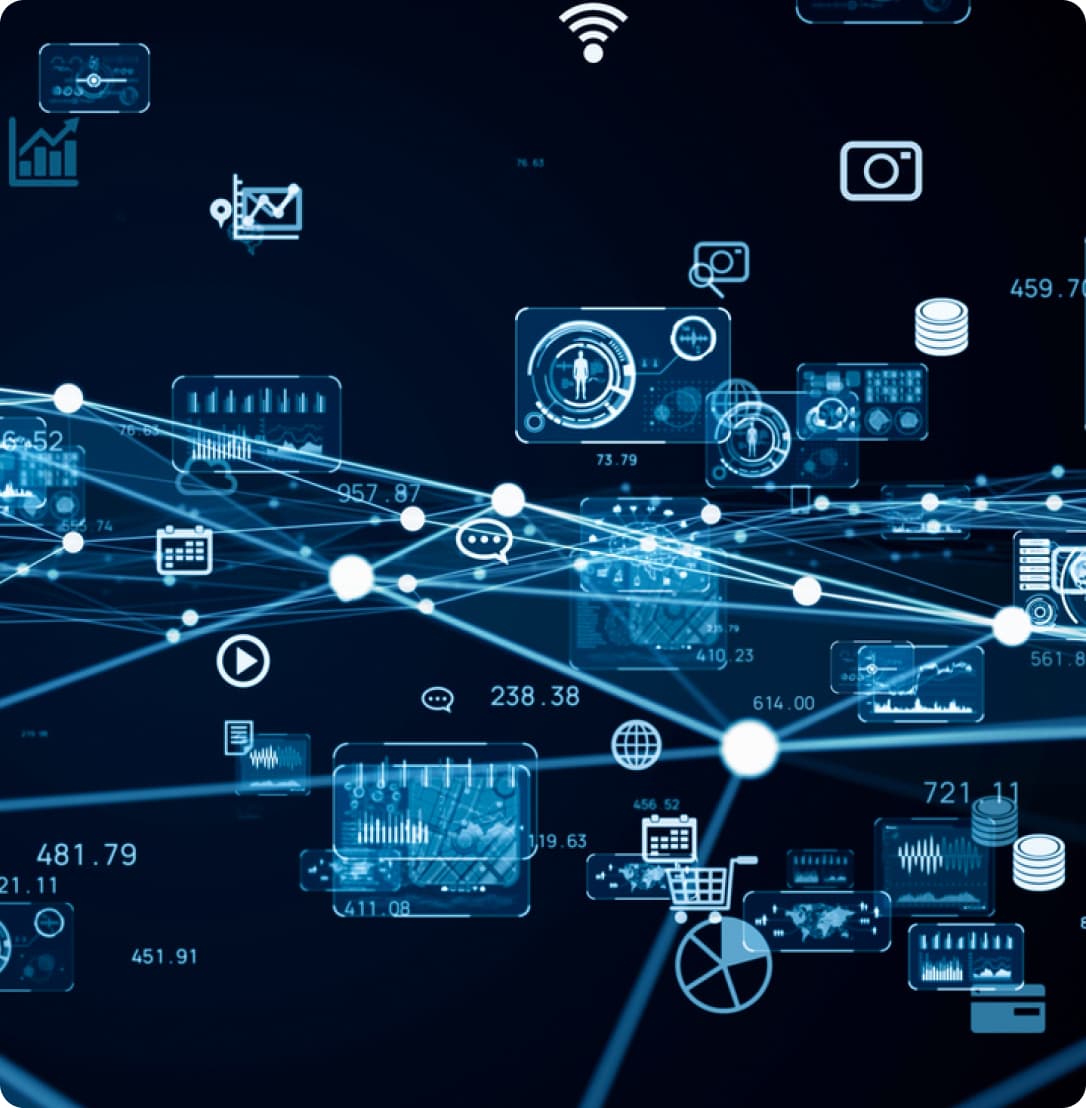
Real-Time Data to Inform Real-Time Decisions
Real-time manufacturing data is one of the most transformational benefits of Industry 4.0 manufacturing. Computers and IIoT machines can continuously process data and provide managers with real-time business insights. For example— if a plant supervisor shuts down a production line due to a defective part, they can quickly isolate which supplier it came from and issue a corrective action.
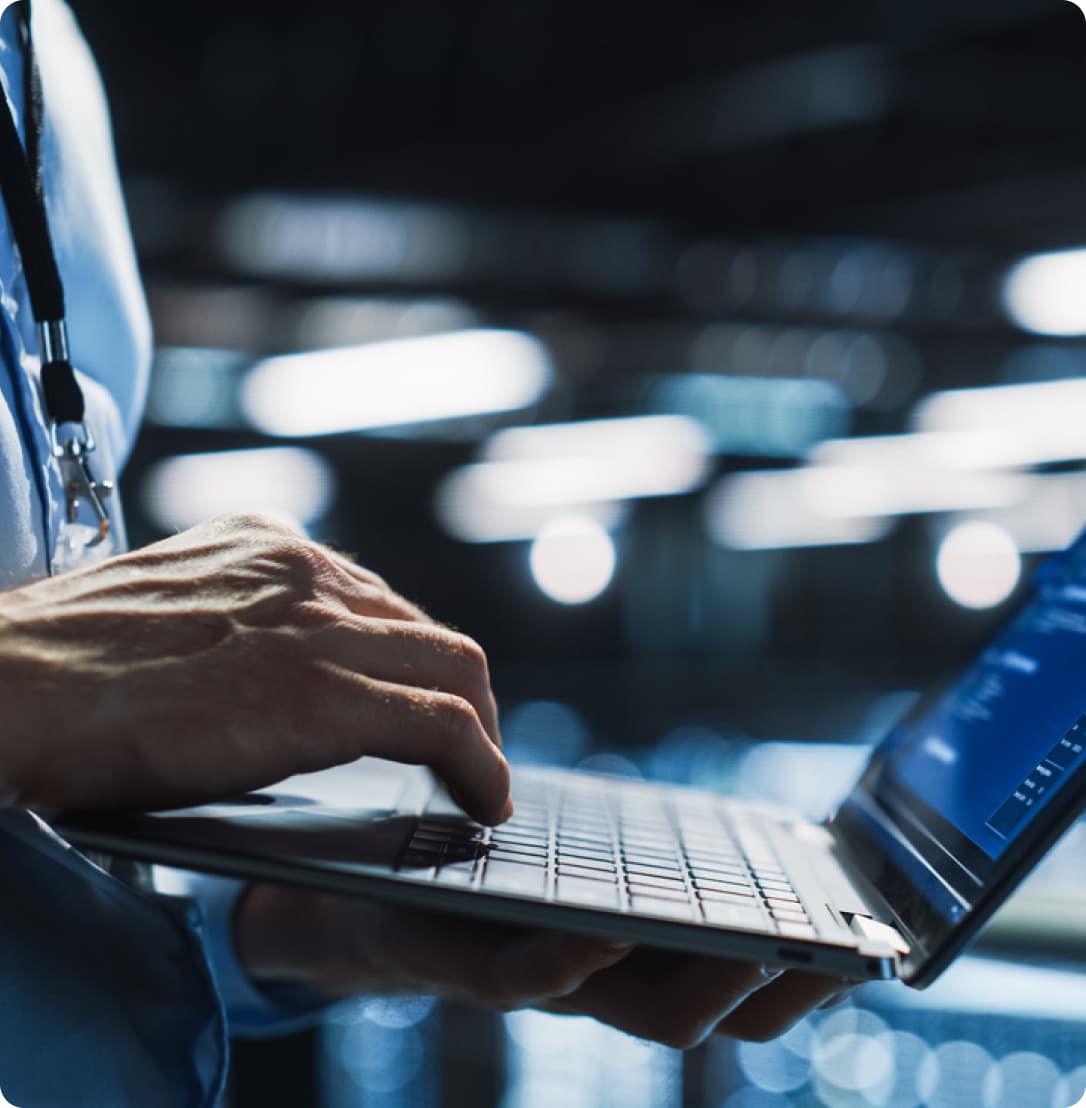
Compliance in Regulated Industries
Industry 4.0 MES enables users to accurately record and search all compliance-related data in case of audits or other traceability purposes. Organizations gain resilience by keeping all traceability accurate and in one place. If production needs to be shut down until a compliance issue is resolved, the right MES is the tool to quickly resolve the problem and prevent downtime.
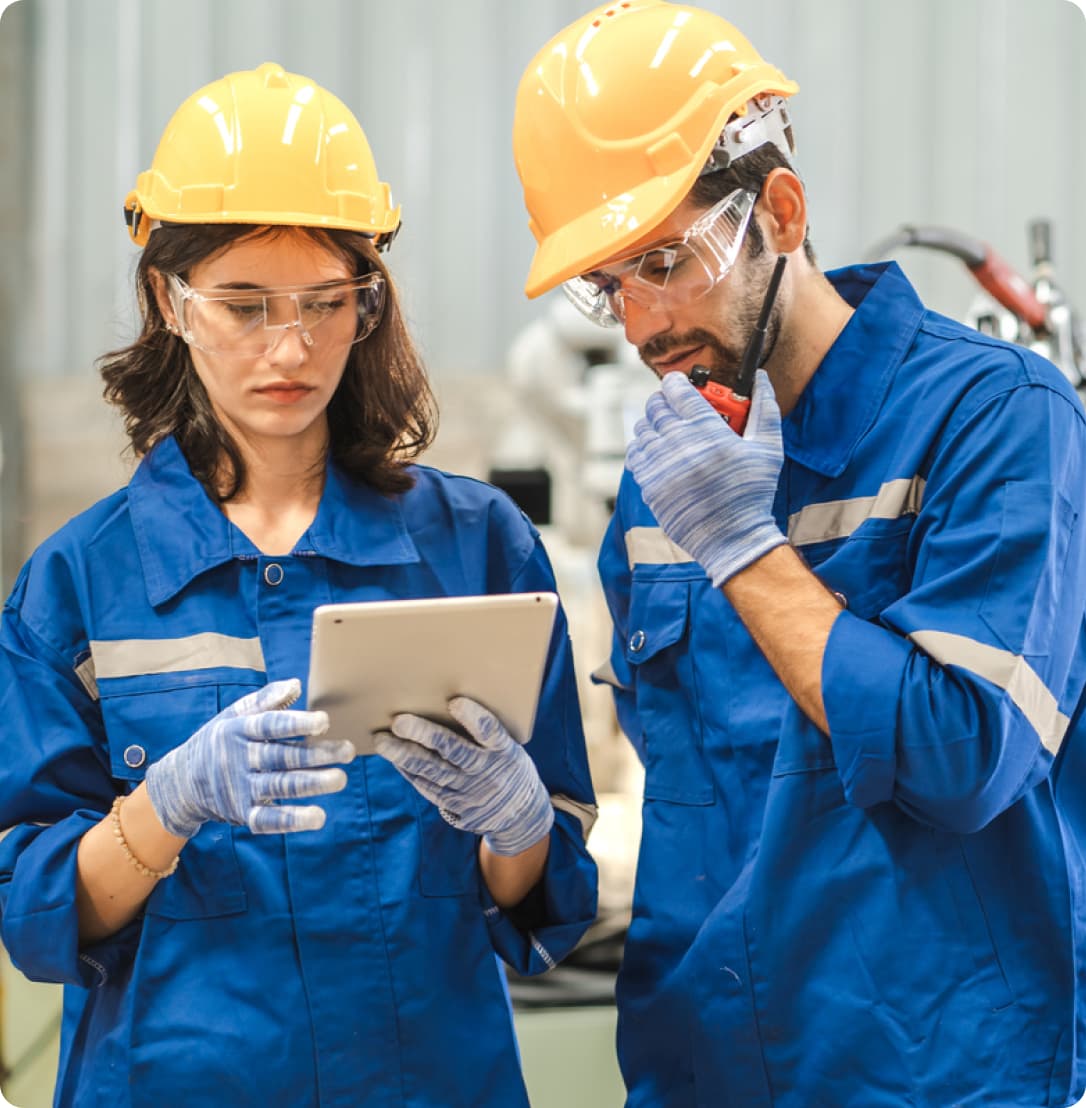
Quality in an Industry 4.0 World
Quality standards have risen as more manufacturers adopt higher expectations. Industry 4.0 manufacturers need high-quality, innovative products. The cascading effect of closed-loop integration, real-time data, machine connectivity, and process automation all work together to reduce errors, downtime, or any other threat to quality and on-time production.
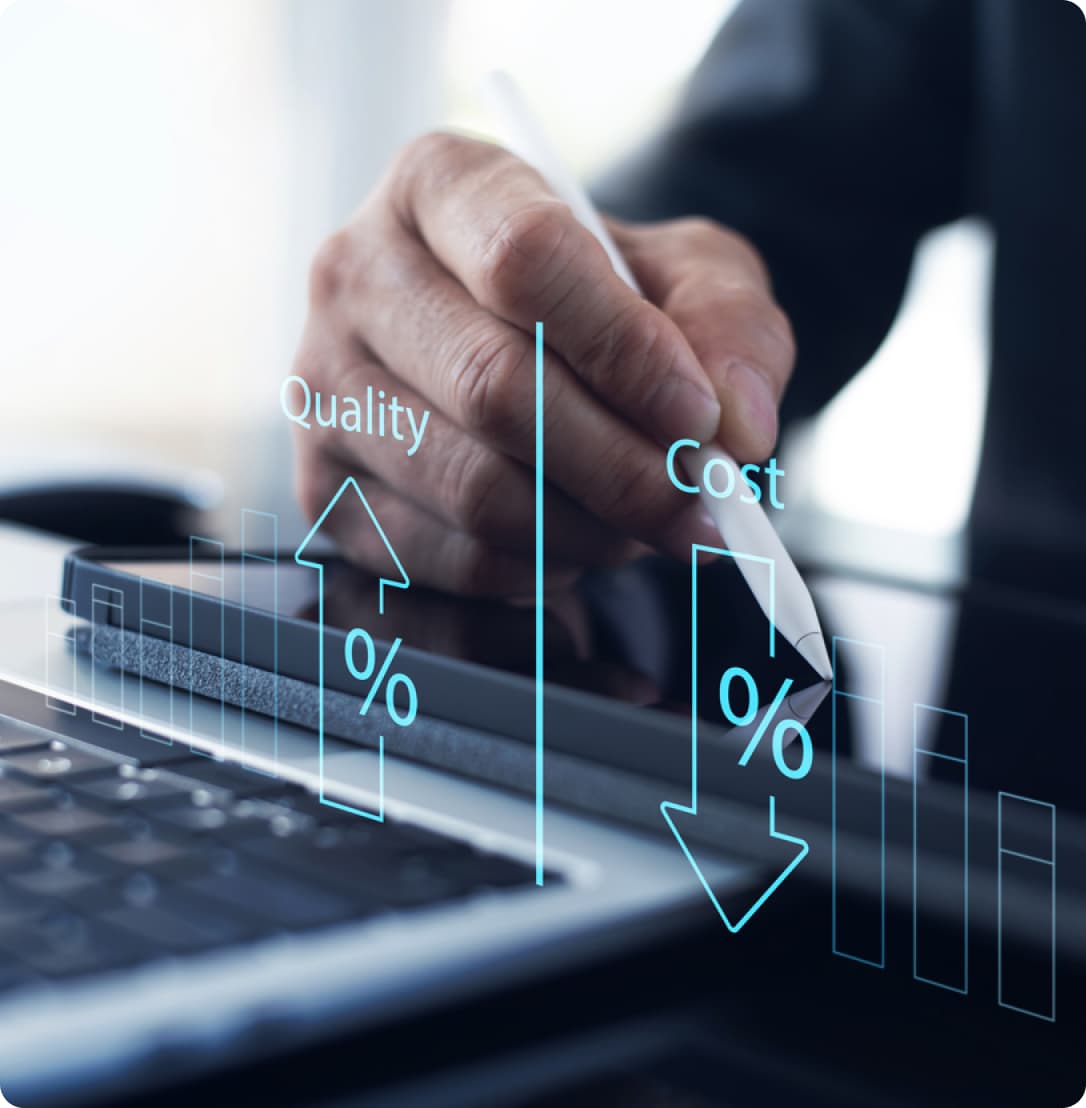
Industry 4.0 Systems Drive Increased Revenue
Increased revenue is the ultimate result of Industry 4.0 MES. Industry 4.0 manufacturers operate with lowered production costs because of real-time data and closed-loop integration. Compared to the last decade, they have decreased cycle times, faster time-to-market, reliable on-time delivery, and higher production capacity.
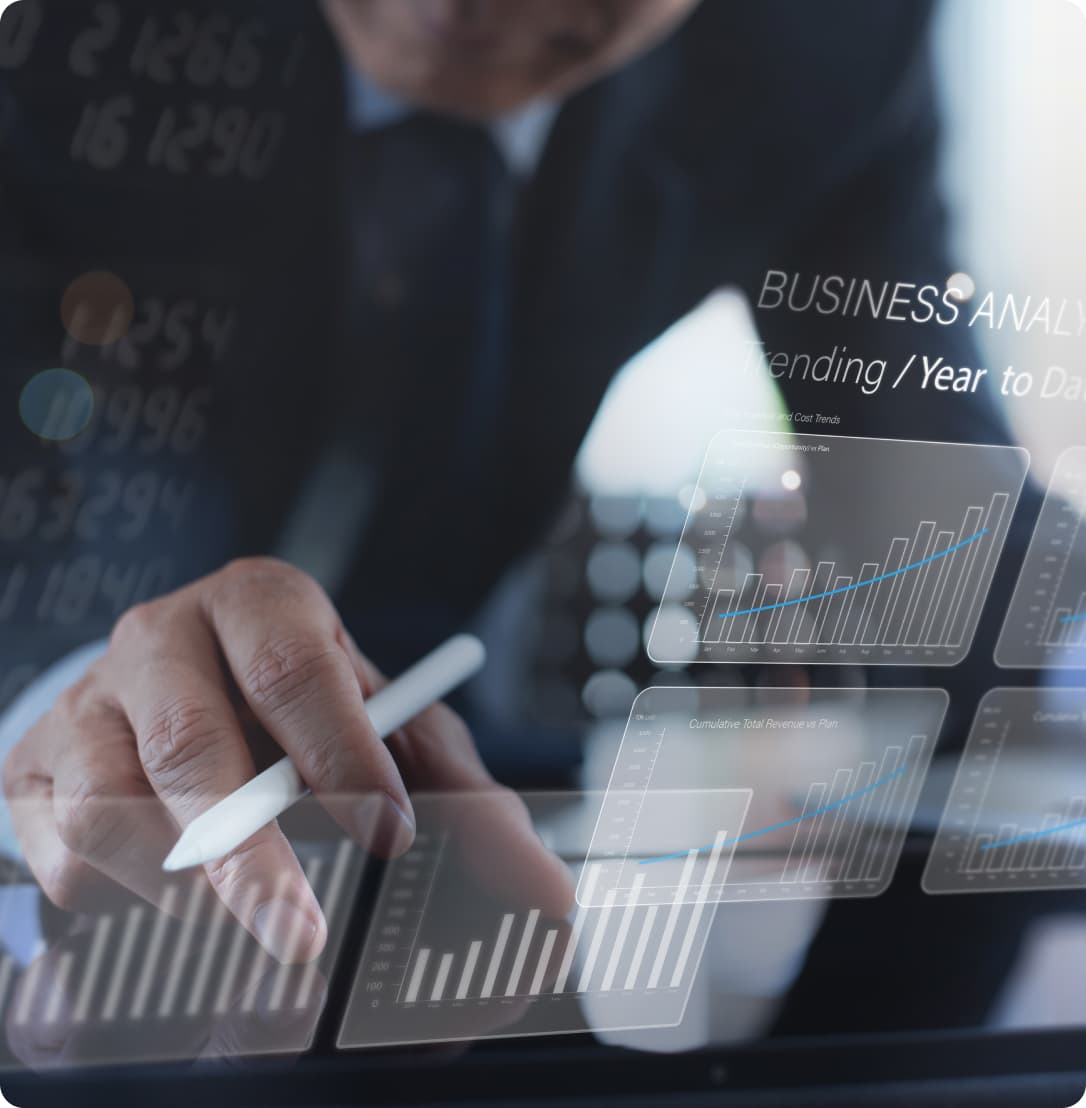
Your Road to Digital Transformation
Digitally transformed manufacturers will need new metrics to measure the success of their digital transformation. As expectations rise higher and higher, what was once considered a gold standard of digital technology is now the norm. Industry 4.0 is a revolutionary change, and that means organizations will also need to change how they measure its success.
Speed of Response
With systems in place that are able to monitor machine performance, quality, or maintenance before they occur, speed of response becomes an important metric. Old metrics, such as Mean-Time-Between-Failure or First-Pass Yield, become less meaningful once downtime, out-of-spec production, and production upsets are essentially eliminated. The new focus of attention becomes the frequency and time between issues, and how quickly the organization can use real-time data to isolate production or supply issues.
Speed of Deployment
The best Industry 4.0 MES solutions have timely implementations. New metrics to measure digital transformation success should include some key indicators:
- Engineering change management cycle time reduction
- Reduced out-of-stock delays in production operations
- Increased ability to handle additional product variants
Rate of Adoption
The earliest metric of digital transformation success is to determine how many business processes are digitally enabled, and how effectively it has improved the processes. As companies plan their Industry 4.0 MES implementation, they should define how processes are done pre-digitalization in order to track the number of processes that move to digital and the speed of adoption. Some new adoption rate metrics include:
- Percentage of manual data entry operations eliminated
- Percentage of reporting operations automated
- Percentage of positions that utilize new technology
- Reduction rate of data entry errors
Exclusive Report: Building a Model-based Enterprise
iBase-t provides research offering insights for manufacturers looking to integrate their tech stack and evolve into a Model-based Enterprise.
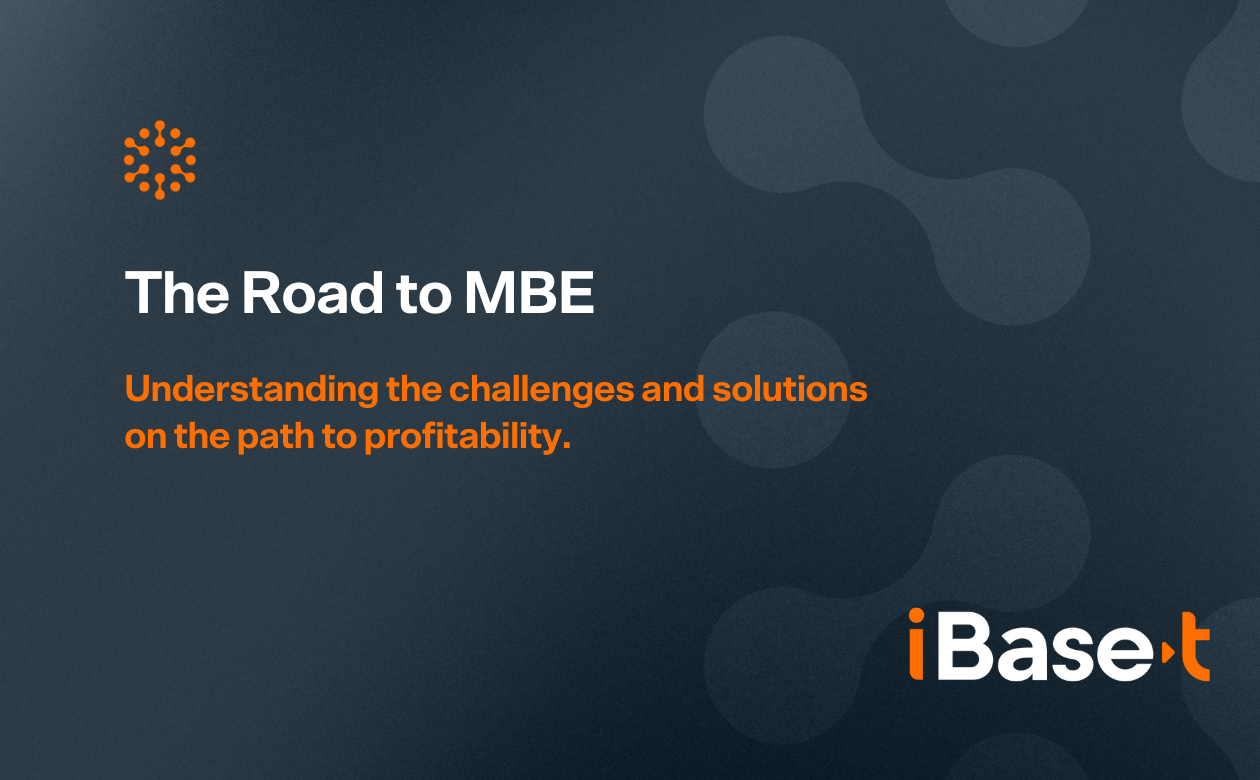
More from iBase-t on MES, Industry 4.0 and Digital Transformation
Learn What Solumina MES
Can Do for You With a Custom Demo